The large-scale welding gear carburizing and quenching process is in the development and test stage of the domestic heavy machine enterprises, and the process is unstable. With the development of domestic large-scale reducers, in order to reduce material costs, welding gears are increasingly used in design. Therefore, the research on the carburizing and quenching process of hard-toothed welded gears will become a major topic in the heat treatment profession, and it has great potential for development.
Since the gear is welded by 20CrNi2MoA ring gear, Q235 web and 35 steel wheel hub, the expansion coefficients of the three materials and the weld material are inconsistent. During the long-term heating of carburizing high temperature and subsequent quenching and cooling, the weld seam is very easy to appear. Cracking and gear deformation. Therefore, the scientific, reasonable and feasible carburizing and quenching process and operating process specifications are formulated. Under the premise of ensuring surface hardness, effective hardened layer depth and metallographic structure, avoiding weld cracking and controlling gear deformation is the main research of this paper. content.

1. Process plan and implementation
Firstly, starting from the technical preparation, the technical requirements of the quality of gear welding are put forward. According to the complexity and technical requirements of the structure, the corresponding heat treatment process documents are developed in a targeted manner. Then, a single-piece test is used to formulate a test plan and technicians. On-site tracking and guiding operation; finally, the test piece is tested according to the pattern requirements, and the gear deformation is actually measured. According to the test result, the feasibility and existing problems of the process are repeatedly demonstrated, and the carburizing and quenching process and the operating process specification are finally formed.
2. Process preparation
According to the process of conventional carburizing and quenching parts, the heat treatment scheme is finally determined, and the welding position is protected technically, the exhaust hole is opened on the web, and the heating rate is controlled to control deformation and cracking.
The Q235 web is a hollow structure. Heating and cooling in a closed space will deform the web due to heat absorption and loss, resulting in cracking of the weld. To reduce this tendency, vent holes are opened on the web.
Due to the inconsistent coefficient of linear expansion of the three materials of the welding gear and the weld material, the weld seam is easily torn due to thermal stress and tissue stress during the heating process, and the Q235 web is hollow, which is prone to deformation during heating. Causes the entire gear to deform. Therefore, the temperature rise rate and the stepwise temperature rise are adopted to reduce the tendency of the workpiece to be deformed due to a large temperature difference between the inside and the outside, and the weld is cracked. High temperature tempering can decompose martensite and retained austenite. Carbon and alloying elements in the layer are precipitated as carbides, which is convenient for cutting and quenching the amount of retained austenite in the layer after quenching. Fully release the thermal stress and the tissue stress during the carburizing process, reduce the deformation superposition and the tendency of the weld cracking, and temper the workpiece after carburizing. The specific carburizing and subsequent heat treatment processes are shown in Fig. 1, Fig. 2, and Fig. 3.
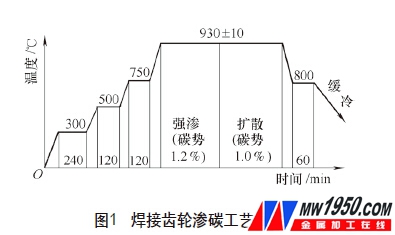
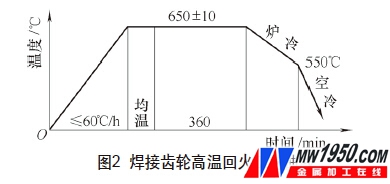
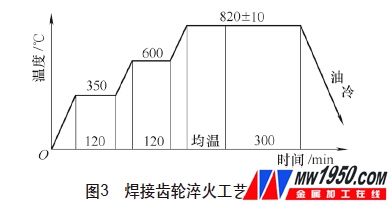
3. Test results
(1) Hardness test Use the fine grinding wheel to grind the carburized and quenched gear teeth to achieve the smoothness of the hardness. Use the HLN-11A type Leeb hardness tester to detect the surface hardness and hardness of the gear tooth in the 120° direction of the gear circumference. For the 54 ~ 56HRC, the technical requirements of the pattern are achieved. The specific test data can be found in the attached table.
In order to understand the carbon concentration and hardness distribution of the carburized layer of the workpiece, the furnace sample was ground and polished, and the hardness gradient of the effective hardened layer was measured by HXD-100TM microhardness tester. The test results are shown in Fig. 4.
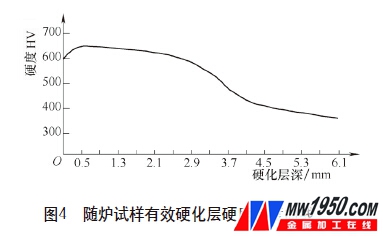
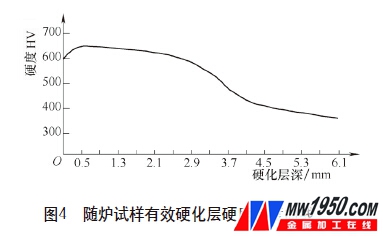
It can be seen from Fig. 4 that the hardness gradient of the effective hardened layer of the carburized part is relatively flat, indicating that the workpiece has been diffused for a long time during the production process, the carbon concentration gradient is relatively gentle, and the effect of the strong expansion ratio of 3:1 is ideal. Such a hardness gradient distribution not only ensures the high hardness and high strength of the layer, but also smoothly transitions with the hardness of the substrate, avoiding the steep gradient of the hardness of the layer and the matrix, and the strength drop is large, causing the layer to peel off.
It can also be seen from Fig. 4 that the effective hardened layer has a depth of 3.2 mm, that is, a depth from the surface to 550 HV, and the core hardness is about 37 HRC.
In summary, the effective hardened layer depth, tooth surface hardness and core hardness have reached the technical requirements.
(2) Metallographic structure After grinding and polishing the furnace sample after quenching and tempering, it is etched with 4% nitric acid alcohol solution, and the metallographic structure is observed under HXD-100TM microhardness tester according to JB/T6141. The .1.6141.4-1992 standard provides a rating for metallographic organization. The metallographic organization is shown in Figure 5.
It can be seen from Fig. 5 that the carbide is a dispersed particle (Grade 3), which is the result of long-term diffusion of the workpiece, which is beneficial to improve surface wear resistance and contact fatigue strength; needle martensite And a small amount of retained austenite structure (Grade 3), indicating that the dispersed carbides are precipitated from austenite during high-temperature tempering, and the degree of alloying in the austenite formed during subsequent quenching is reduced, and the residual austenite is reduced. The volume is beneficial to improve the surface hardness and strength of the workpiece, and at the same time reduce the structural stress caused by the residual austenite transformation during the grinding process, and reduce the tendency to produce grinding cracks; lath martensite and a small amount The core structure of ferrite (grade 3) ensures that the workpiece has a high core strength and avoids failures such as broken teeth during work. This structure also matches the hardness of the heart around 37HRC, metallographic structure. All met the technical requirements.
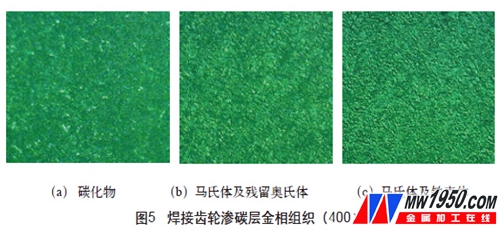
(3) Deformation detection The machine-related detection equipment detects the common normal line deformation ≤0.4mm, the tooth top circle deformation ≤0.5mm, the end surface warpage amount ≤2.0mm, and various deformation data are within the process retention range, and it does not appear. Defects such as cracks, the quality is ideal.
4. Conclusion
Practice has proved that it is feasible to open the vent hole and weld seam protection on the web, and to control the heating rate and stepwise temperature rise to prevent weld cracking and gear deformation. A strong expansion ratio of 3:1 can effectively control the carbon concentration gradient of the layer and improve the metallographic structure of the layer. High temperature tempering and single-piece quenching after carburizing can effectively control weld cracking and gear deformation.
   About the author: Liu Min, Mining and Metallurgical Equipment Branch of Northern Heavy Industry Group Co., Ltd.; Yan Liang, Li Wei, Zhao Wei, Heat Treatment Branch of Northern Heavy Industry Group Co., Ltd.; Sun Zhitao, Shenyang Huibo Thermal Energy Equipment Co., Ltd.
Car Polisher,Car Wax,Car Wax Polish,Mini Polisher
Foshan SUMEITE Grinding Technology Co.,Ltd , https://www.aedetail.com