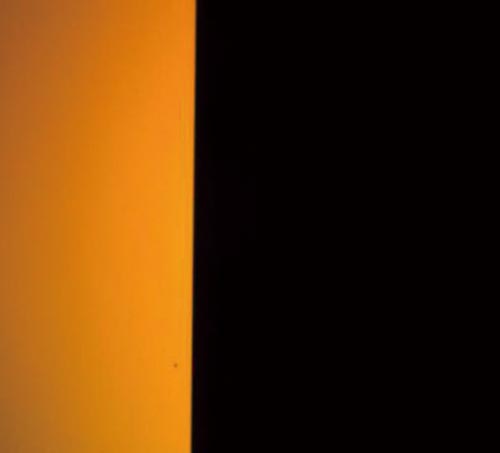
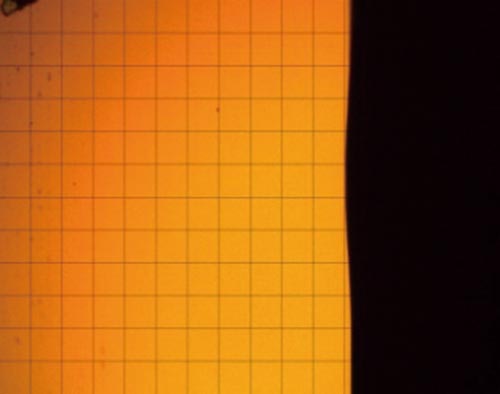
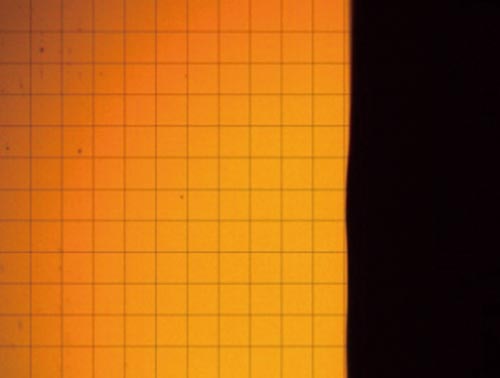

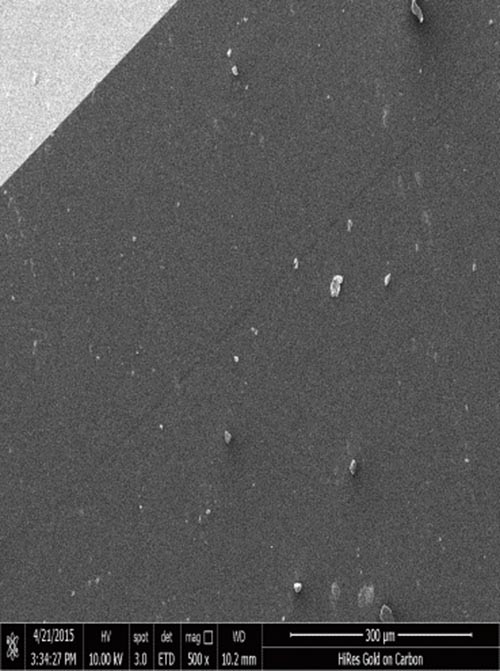
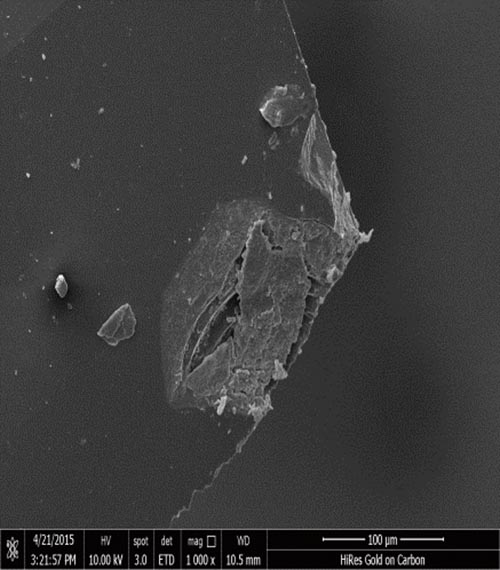
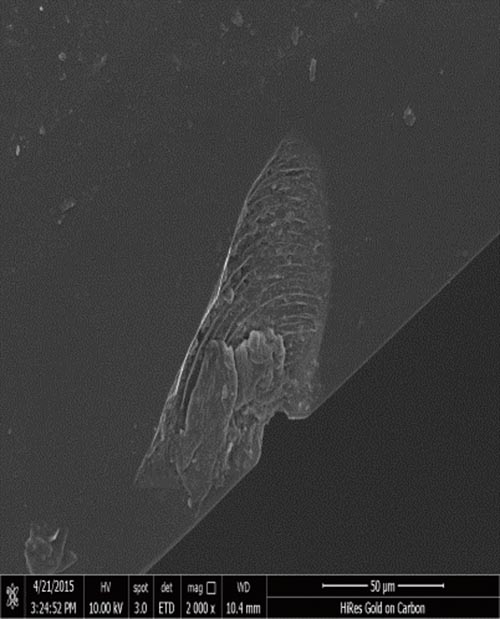
EVA Colorful Building Blocks is consist of four different but classical colors. Made from Eco-friendly, closed cell, non-smell and non-toxic Eva Foam material, passes ASTM and EN71 certificates, the safety of this product is the last thing needs to be worried.
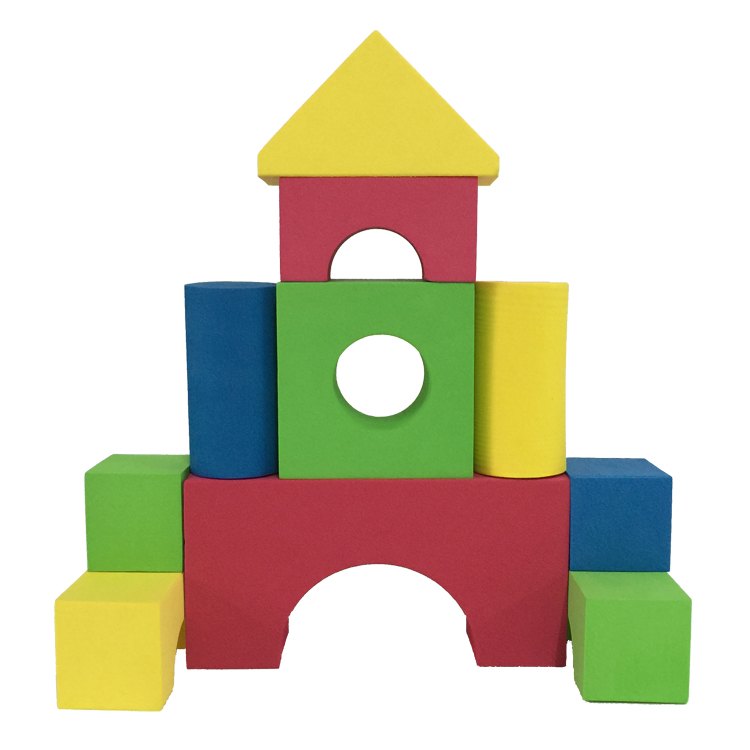
The Foam Building Blocks are easy to store and carry cause it is packed with a PVC bag with zipper. Also after a long time of playing, the blocks can be cleaned easily with water thanks to its closed cell foam.
Eva Colorful Building Blocks,Colorful Building Blocks,Colorful Eva Foam Building Block,Eva Colorful Foam Building Block,Colorful Foam Building Block,Colorful Educational Building Block
Huizhou Melors Plastic Products Factory , https://www.melorsfoam.com